Industrial Coatings Industry: Maintenance, Removal, & More
Add a headline.
Lorem ipsum dolor amet food truck affogato cronut freegan skateboard photo booth, tousled pickled 90's wayfarers retro succulents hoodie edison bulb ramps. XOXO seitan tote bag, offal vape air plant disrupt chia plaid taxidermy cloud bread microdosing 8-bit.
What are industrial coatings
- Epoxy Coatings: Known for chemical resistance and strong adhesion, epoxy industrial coatings are commonly used in industries like manufacturing to protect steel and concrete surfaces from wear and chemical damage. These industrial coatings are also widely used as floor coatings in industrial facilities. Read more about how to remove epoxy in this blog.
- Polyurethane Coatings: These coatings are flexible and highly resistant to abrasion, making them ideal for applications in automotive parts, machinery, and outdoor equipment. These types of industrial coatings provide long-lasting protection against wear, chemicals, and UV light degradation.
- Zinc-rich Primers: Often used in steel structures, such as bridges and pipelines, zinc-rich primers provide robust corrosion protection by acting as a sacrificial barrier, preventing rust formation and extending the life of the underlying metal.
- Acrylic Coatings: Acrylic coatings offer specialized weatherability, UV resistance, and color retention, making them ideal for use on outdoor signage, decorative finishes, and architectural coatings.
- Intumescent Coatings: These coatings expand when exposed to high heat, creating an insulating layer that protects structural steel from fire damage. They are commonly used in buildings and industrial plants for fireproofing purposes.
- Polyurea Coatings: Known for their rapid curing time and extreme durability, polyurea coatings are used in applications that require high resistance to impact, chemicals, and abrasion, such as in mining equipment, water treatment plants, and tank linings.
Who Uses Industrial Coatings
How to Remove Industrial Coatings
-
Abrasive Blasting/Dustless Blasting: This involves using materials like sand, glass beads, or steel grit to blast off the industrial coating. It's effective for thick layers of coating and works well on metal surfaces. Sandblasting or media blasting is one of the most common methods for surface preparation before applying new coatings.
-
Chemical Stripping: Chemical removers, such as paint thinner or solvents, can dissolve coatings, making them easier to scrape or wipe off. Chemical adhesive removal or paint thinner is often used for more delicate substrates where abrasive methods might cause damage or when dealing with soft substances such as uncured epoxy.
-
Heat Stripping: Using heat to soften coatings can make them easier to remove. Heat guns or propane torches are commonly used for this, though care must be taken not to damage the underlying material.
-
Mechanical Methods: Scraping, sanding, or grinding can be used to remove coatings manually or with power tools. This is typically slower than blasting or chemical methods but may be necessary for smaller or more precise areas.
The method you choose depends on the coating type, the substrate material, the environment, and the size of the job. After removal, it's essential to thoroughly clean the surface to ensure proper adhesion for high quality coatings.
Preparing a Surface for New Coatings
Once the old coating is removed, proper surface preparation is essential for ensuring high quality coatings and to enhance durability during the application process.
- Start by thoroughly cleaning the surface to remove dust, grease, oil, or contaminants using appropriate cleaners or degreasers.
- If the surface is steel, be sure to remove any mill scale, a layer of oxide that forms from chemical processes during manufacturing, as it can prevent proper adhesion. Removing mill scale can be removed through abrasive blasting or grinding.
- Next, check the surface profile—if it's too smooth, use abrasive blasting or sanding to create the right roughness for adhesion.
- Remove any rust or oxidation with wire brushing or chemical rust removers.
- Ensure the surface is completely dry before applying any coatings to prevent moisture-related issues. If necessary, apply a primer to improve adhesion and corrosion resistance, then allow it to cure fully.
- Finally, perform a final cleaning with a tack cloth to remove any remaining debris before applying the new coating according to manufacturer guidelines, ensuring optimal conditions for curing and adhesion.
Industrial Sandblasters for Coating Removal
One of the most efficient ways to remove industrial coatings is with an industrial sandblaster or dustless blaster. These machines use abrasive materials—like garnet, crushed glass, or coal slag—blasted at high velocity to remove rust, corrosion, and industrial coatings, preparing surfaces for new finishes or repairs. Not all blasters are created equal, what sets each machine apart comes down to a few key factors: volume capacity, the air compressor they’re paired with, and the versatility and mobility of the blasting setup.
Industrial sandblasters have larger drums to hold maximum volume of abrasive or an abrasive and water mixture. This drastically cuts down on time between machine refills and keeps operations efficient. Industrial sandblasters require compressors with higher CFM ratings to maintain consistent pressure, higher PSI to effectively strip thick coatings or corrosion, and a continuous duty cycle for non-stop operation to ensure reliable performance during demanding projects.
When it comes to versatility and mobility of sandblasting setups, Dustless Blasting is industry-leading. With wheeled blast pots, compressor-ready solutions, and comprehensive trailer-mounted units, our sandblasters make it easy for operators to transport their machine to remote job sites and offer maximum versatility with the ability to wet, dry, and soda blast in one machine. Whether you're working on steel structures, offshore rigs, or in a refinery, our industrial sandblasters are built to make coating removal and other surface preparation faster, safer, and easier.
How to Succeed in the coatings industry
The coatings industry offers numerous opportunities, but thriving in this competitive field requires more than just technical expertise—it calls for versatility. Key factors shaping the industry include globalization, corporate consolidation, and the need for innovative solutions. Whether you're an experienced professional or just launching your coatings business, one of the most crucial elements for success is mastering both the removal of old coatings and the precise application of new ones.
Visit this blog to learn more about how to master your skills and find success in the industrial coatings industry.
Industrial Coatings industry FAQs
What About failed polyurea lining removal?
Polyurethane linings are commonly applied to metal, concrete, or other surfaces to protect against corrosion, chemical exposure, abrasion, and extreme temperatures, particularly in industries like mining, wastewater treatment, and oil and gas. Without proper preparation or maintenance, this lining can start to pull away from the surface it has been applied to. The removal process typically involves using specialized abrasive blasting techniques, such as wet blasting or soda blasting with Dustless Blasting, to gently remove the old lining without compromising the surface. In some cases, chemical stripping agents may also be used to break down the polyurethane, making it easier to peel off.
How Do I remove Bed liner?
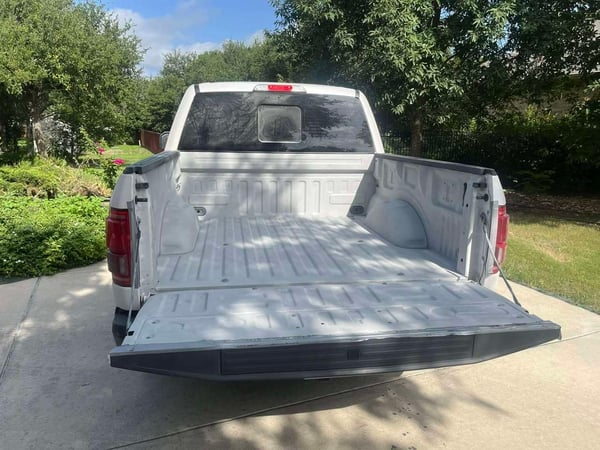
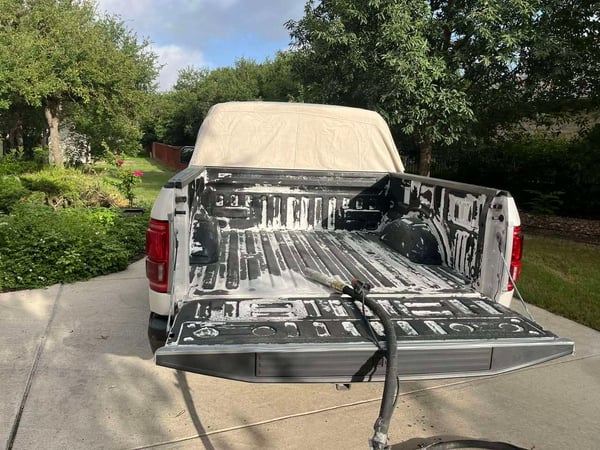
What are industrial powder coatings?
What is the process of removing mill scale?
UPGRADE YOUR SURFACE PREP WITH DUSTLESS BLASTING
Dustless Blasting is at the forefront of the mobile blasting and cleaning industry, offering a dynamic way to control your future and operate a versatile on-site service. Inspired by the substantial potential and demand in the mobile paint stripping and cleaning industry—which is valued at over $10 billion annually and growing—here's why the Dustless Blasting surface preparation method is a preferred choice for providing customers with industry-leading results:
-
Revenue and Demand: Everything around us is painted, rusty, or dirty, and while the demand for cleaning services has a global reach, the supply of providers can be limited, presenting a lucrative market opportunity.
-
Cost-Effective and Quick Start: With our comprehensive mobile systems, you can start your business or add to your existing operation as soon as you drive off the lot. Get a fast track to generating revenue with high margins with no ongoing fees or royalties.
-
Scalability and Support for Startups: The business model supports easy scalability, allowing for expansion through additional trailers and crews. Plus, you gain the advantages of community support, marketing tools, and a reputable brand without the burden of franchise fees.
-
Versatility: Whether you're launching a new venture or expanding an existing one, Dustless Blasting is a smart investment and preferred choice for many surface restoration pros. It's highly adaptable, capable of handling diverse jobs across multiple industries so you can jump into providing customers a one-stop-shop without the use of harsh chemicals.
Next Steps
Ready to take the next step with a versatile, cost-effective dustless blaster? Download our product catalog below or book a meeting with our blast experts to start blasting today!