Dustless Blasting for Plant and Refinery Maintenance
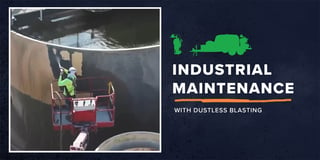
Maintaining refineries and industrial plants, a process called plant maintenance, is crucial for reducing equipment breakdowns, enhancing uptime, and ensuring the reliability of industrial assets. Among various maintenance activities, managing the integrity and functionality of industrial coatings plays a significant role. These coatings protect equipment from corrosion, chemical damage, and wear and tear. However, once their lifespan is over, removing these coatings can pose challenges due to their tough composition and the sensitivity of the substrate beneath. Dustless Blasting emerges as a superior solution for overcoming these challenges with minimal disruption to operations.
Image: Blasting away caked-on coatings and contaminants from a refinery tank.
What is Dustless Blasting?
Dustless Blasting is a cutting-edge surface preparation method that combines water and abrasive materials to effectively remove contaminants, coatings, and other substances from surfaces while minimizing airborne dust. This innovative technique is particularly advantageous in industrial maintenance settings, where traditional methods can pose significant challenges to personnel. By incorporating water into the blasting process, Dustless Blasting minimizes dust production, thereby reducing the risk of inhalation of hazardous particulates. This method not only ensures a cleaner and safer working environment but also enhances surface adhesion of the subsequent new coating by profiling the substrate as it's being cleaned.
Understanding Industrial Coatings
Industrial coatings are specialized coatings applied to surfaces to protect against the harsh conditions within industrial facilities. These coatings prevent rust and corrosion, offer chemical resistance, and improve the durability and aesthetics of industrial equipment in refineries, plants, oil rigs, and other similar environments.
Common Types of Industrial Coatings
-
Industrial Epoxy coatings: Known for chemical resistance and strong adhesion to surfaces. See our blog on how to remove epoxy coatings.
-
Polyurethane coatings: Offer high abrasion resistance and flexibility.
-
Zinc coatings: Provide robust corrosion protection, often used as primers in steel structures.
Image: Paint and primer layers revealed after a quick blast. Offshore Drilling Rig, utilizing Dustless Blasting equipment.
Importance and Challenges of Coatings
Over time, even the most resilient coatings deteriorate. Factors like weather, chemical exposure, and mechanical stress degrade their effectiveness. When these coatings need replacing, thoroughly removing the old layer without damaging the substrate is essential, yet challenging. This process must be
-
efficient to minimize downtime
-
minimally disruptive so as to not interfere with ongoing operations
-
gentle on industrial machines so as to prevent failures and maintain reliable operation
Importance of Maintenance in Refineries and Plants
Maintenance is the backbone of safe and efficient operations in refineries and plants. Regular and well-planned maintenance activities are crucial for preventing equipment failures, reducing downtime, and minimizing the risk of accidents. In the high-risk environment of refineries, where processes involve hazardous materials and complex machinery, the importance of a robust maintenance program cannot be overstated. A meticulously planned maintenance program helps identify potential issues before they escalate into costly repairs or catastrophic failures. By proactively addressing maintenance needs, facilities can ensure continuous operation, safeguard their workforce, and maintain compliance with stringent safety regulations.
Image: Dustless Blaster prepping tanks at Water Treatment Plant for application of new industrial coatings.
Industrial Maintenance Strategies
Implementing effective maintenance strategies is essential for the reliability and efficiency of equipment and processes in refineries and plants. Various maintenance strategies can be employed to achieve these goals, including preventive maintenance, predictive maintenance, and reliability-centered maintenance (RCM).
Preventive Maintenance
Preventive maintenance is a proactive approach that involves performing regular maintenance tasks to prevent equipment failures and reduce downtime. Inspection-driven preventive maintenance aims to minimize unplanned events in refinery maintenance programs. This strategy is typically based on the manufacturer’s recommendations or the equipment’s operating history. Preventive maintenance tasks may include cleaning, lubricating, inspecting equipment, and replacing worn or damaged parts and coatings. By adhering to a preventive maintenance schedule, facilities can extend the lifespan of their equipment, enhance operational efficiency, and prevent unscheduled shutdowns.
Predictive Maintenance
Predictive maintenance leverages advanced technologies such as sensors and data analytics to predict when equipment is likely to fail. This approach allows maintenance technicians to schedule maintenance tasks in advance, thereby reducing the risk of unexpected downtime, unnecessary maintenance costs and equipment failures. Predictive maintenance is particularly beneficial in refineries and plants, where equipment failures can have significant consequences. By installing predictive maintenance measures, facilities can optimize their maintenance programs, improve asset management, and ensure the reliability of critical assets.
Reliability-Centered Maintenance (RCM)
Reliability-centered maintenance (RCM) is a strategic approach that focuses on identifying and addressing the root causes of equipment failures. RCM involves analyzing equipment failure data to identify patterns and trends, and then developing maintenance strategies to address these issues. This method is especially useful in refineries and plants, where equipment failures can lead to severe operational disruptions. By implementing RCM, maintenance technicians can enhance their maintenance strategies, improve the reliability of their equipment, and minimize maintenance costs.
By employing these maintenance strategies, refineries and plants can significantly reduce downtime, improve efficiency, and minimize the risk of accidents. Regular maintenance is essential for ensuring the safe and efficient operation of equipment and processes, and it plays a critical role in extending the lifespan of critical assets.
The Role of Dustless Blasting in these Strategies
Dustless Blasting introduces a groundbreaking solution for efficiently removing industrial coatings. Unlike traditional sandblasting, Dustless Blasting combines water and abrasive media, reducing friction and heat during the removal process. Here's how it transforms industrial maintenance:
How Dustless Blasting Works
Dustless Blasting systems utilize high-pressure streams that mix water and abrasive materials to safely strip away coatings. This method is capable of effectively removing even the toughest coatings without harming the substrate, ensuring surface integrity and quality adherence of fresh coatings.
Advantages of Dustless Blasting in Refineries and Refinery Maintenance Programs
-
Dust Suppression: Water suppresses the formation of dust plumes, enhancing safety and reducing air contamination, which is crucial in industrial working environments.
-
Efficient Coating Removal: Water improves the force of the blast abrasive, enabling quicker coating removal compared to traditional dry sandblasting. This enables easy removal of multiple layers of coatings, sealers, primers, and other contaminants. This efficiency boost enabled by the inclusion of water helps to minimize labor cost and time spent on performing surface maintenance.
-
Simultaneous Surface Profiling: Blasting, being an inherently abrasive process, allows the operator to prepare their substrate with a profile ideal for adhesion, which eliminates the need to sand or roughen the surface afterwards with an additional step. If not desired, this abrasive aspect of Dustless Blasting can be mitigated by using a round abrasive such as glass bead or sugar sand.
-
User-Friendly Operations: Dustless Blasting equipment is designed for ease of use, which helps to reduce the time required to train personnel on proper operation, maintenance, and repair. We utilize a simple system design with few wear parts and ZERO proprietary valves, meaning cheaper replacement parts and greater purchase options for the equipment owner.
Case Studies and Real-World Applications
The practical benefits of Dustless Blasting have been demonstrated in various industrial applications. Here are two notable examples:
Case Study: Water Treatment Plant Revamp
Pro Blasting of South Florida and Surface Prep Pros, LLC utilized Dustless Blasting on a large-scale water treatment plant. With three machines operating simultaneously, they removed coatings and applied fresh epoxy layers efficiently. The dust-suppression feature allowed other contractors to continue work nearby, showcasing Dustless Blasting's ability to streamline complex projects while ensuring safety and compliance.
SEE IT IN ACTION: Tackling Industrial Glue Removal
Dustless Blasting was employed to remove industrial-strength adhesives that traditional blasters couldn't tackle. With the reduction of heat and friction, staff effectively stripped away glue layers without damaging the surfaces beneath. For a visual overview of the process, view the video demonstration here.
SEE IT IN ACTION: REMOVING MILL SCALE
Mill scale is a tough layer of iron oxides and magnetite which coats the surface of hot rolled steel. It is necessary to remove mill scale before welding or painting can occur, but the process is usually difficult and time consuming. Our process eliminates mill scale quickly and efficiently, leaving a white metal finish.
Learn how to easily remove mill scale with our equipment.
Charting the Future of Predictive and Preventive Maintenance
Given the benefits and versatility of Dustless Blasting, it’s poised to radically change maintenance practices across industrial maintenance applications. Its efficiency, environmental benefits, and ease of use make it an attractive option for refineries and plants aiming to enhance operational efficiency, safety, and sustainability. Striving to improve refinery maintenance programs is crucial for maintenance and repair of complex equipment and systems, and Dustless Blasting can play a significant role in this effort.
If you’re looking to optimize your facility’s preventive maintenance, consider exploring how Dustless Blasting can benefit your operations. For further information and personalized insights, contact our experts today to learn more about integrating this technology into your business.