How to Remove Epoxy: Industrial Methods
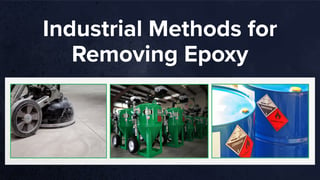
Epoxy is a tough, long-lasting material commonly used in industrial settings for coatings, adhesives, and structural applications. While its durability makes it ideal for a wide range of uses, there are times when epoxy removal becomes necessary—whether it's to remove worn-out epoxy flooring, clean up excess resin from a project, or strip coatings from machinery. For industrial environments, removing epoxy efficiently and without damaging the underlying surface is crucial, and the right method can save you time and money. In this blog, we'll guide you through the most effective techniques for how to remove epoxy in industrial settings, covering everything from mechanical and chemical methods to the versatile advantages of Dustless Blasting.
Heat and Scrape
When considering how to remove epoxy for smaller surface areas, heat can be a highly effective method for spot removal of hardened epoxy coatings or uncured epoxy, especially in situations where chemical or mechanical methods are less feasible. Heat guns are commonly used to apply concentrated heat directly to cured epoxy, typically in the range of 300°F to 500°F (150°C–260°C). This high temperature softens the resin, making it more pliable and easier to scrape off with metal or plastic tools. Heat is particularly useful for smaller or localized applications, such as removing epoxy from surfaces like wood or concrete and other intricate components, where other methods to remove epoxy may risk damage to a larger surface area.
However, while effective for smaller patches, a heat gun can be slow and labor-intensive when dealing with large areas or multiple layers of epoxy or epoxy glue, as it requires working in small sections at a time. The process can also be less efficient for thick or heavily adhered coatings, where mechanical or abrasive methods would typically offer faster, more productive results. For industrial-scale epoxy removal, heat is generally not the primary method for large areas. Instead, mechanical methods like grinding or shot blasting are more efficient for handling large surfaces or deep epoxy layers.
When using heat to soften epoxy, it's important to take precautions to avoid overheating the underlying surface. Excessive heat can damage the substrate, especially if it is wood, plastic, or other sensitive materials. Heat should be applied evenly and controlled, ensuring that the temperature doesn’t exceed the threshold that could cause harm to the surface below.
Important Safety Note: A heat gun should never be applied to surfaces that have acetone, paint thinner, or denatured alcohol on them. The combination of heat and flammable substances can pose a serious fire hazard. Always ensure the surface is free of any volatile solvents before applying heat.
Mechanical Removal
In industrial environments where epoxy coatings are thick, heavily adhered, or cover large surface areas, such as industrial epoxy flooring, mechanical removal is often necessary to efficiently strip the material. Power tools like grinders, scarifiers, or scrapers are designed to tackle tough, large-scale applications and are a common choice for removing industrial-grade epoxy coatings. When considering how to remove epoxy with a mechanical method, the choice of tool will depend on the size of the area, the adhesion strength of the epoxy, and the desired finish, with each tool offering distinct advantages based on the project requirements.
Because these methods generate significant dust and debris, proper safety measures are crucial. Always wear appropriate protective gear, including a dust mask, gloves, and goggles. Additionally, utilizing dust control systems, such as a vacuum or water attachment or dust-collection-equipped tools, helps mitigate health and safety risks in the work environment.
Here’s an overview of some of the most effective industrial tools for epoxy removal:
-
Rotational Grinders: Grinders equipped with carbide chips or PCDs (Polycrystalline Diamonds) are ideal for aggressive removal of thick, well-adhered epoxy or heavy duty bonding adhesive on industrial-sized concrete floors. Rotational grinders, which can be used wet or dry (with a vacuum for dust control), may etch the floor surface when using PCDs, requiring follow-up sanding or grinding to achieve a smooth or other desired finish.
-
Scarifier: This drum-based tool is highly effective for removing thick coatings like epoxy resins, particularly in large industrial areas where the epoxy is deeply adhered. The scarifier uses rotating blades or flails to aggressively chip away at the material, making it ideal for fast, high-volume removal on hard, durable surfaces such as concrete, asphalt, stone, and certain industrial-grade tiles. However, because of its powerful chipping action, the scarifier can leave behind a rough, uneven surface, often requiring additional preparation like sanding or grinding to achieve a smooth finish. Despite this, it's a go-to choice for high-production environments where quick and effective coating removal is needed.
-
Floor Scraper: A floor scraper is a powerful tool equipped with a blade designed specifically for scraping epoxy from an epoxy stained surface such as concrete or industrial flooring. This method is one of the fastest options for industrial-scale epoxy stripping, making it ideal for situations where speed and efficiency are crucial. Floor scrapers generally leave the surface clean and free of debris, typically eliminating the need for follow-up smoothing, unless the floor itself is damaged or uneven.
-
Shot Blasting: Ideal for heavy-duty cleaning and coating removal, shot blasting uses metallic beads or pellets propelled by centrifugal force to clean floors and remove coatings. This method of removal is typically used to remove hardened epoxy but may be less effective to revue epoxy resin that is still pliable or soft. Unlike sandblasting, shot blasting uses metal particles and is not suitable for delicate surfaces but is highly effective for tough, thick layers.
Chemical Removal
For more delicate applications or when mechanical methods are insufficient, chemical solvents can effectively remove epoxy. Solvents like acetone or paint thinner, methylene chloride, and specialized epoxy removers break down the resin’s structure, making it easier to lift and wipe away. While they work best on soft epoxy, they can also remove fully cured epoxy resins with extended exposure and multiple applications.
Always work in a well-ventilated area and wear protective gloves, goggles, and respiratory gear, as solvents can be hazardous. In industrial applications, soaking the part in solvent or paint thinner can be especially useful when mechanical or heat methods alone aren’t feasible. Soaking causes the epoxy to expand and soften, making it easier to remove. Acetone or paint thinner is commonly used first, but for thicker layers or fully cured epoxy, stronger chemicals may be needed.
When using stronger solvents, always test or gently rub them on the substrate first to ensure they won't damage sensitive materials like plastic, wood, or painted surfaces. In order of increasing aggressiveness, solvents can be used as follows:
-
Acetone (most common and least aggressive)
-
Toluene (stronger, may require longer exposure)
-
MEK (Methyl Ethyl Ketone) (effective for tougher coatings)
-
Sulfuric Acid (strong, use with caution)
-
Methylene Chloride (highly effective but dangerous—use for industrial applications only)
These solvents are typically more effective for smaller-scale applications or intricate components. For large-scale industrial work, chemical removal is often used in conjunction with mechanical methods for more efficient results.
Important Safety Note: Always test on a small area before submerging the entire part in any solvent, as some chemicals can cause irreparable damage to the surface or the material beneath the epoxy. Additionally, be cautious when using chlorinated solvents like methylene chloride, as they are highly toxic and require proper ventilation and protective gear.
Dustless Blasting
For large or complex surfaces, Dustless Blasting is an effective and versatile method for removing cured epoxy. By combining abrasive media with water, Dustless Blasting significantly reduces airborne dust, improving visibility and cooling the underlying surface during the removal process. This makes it ideal for larger projects with substrates like metal or concrete, where excessive heat or abrasion could cause damage. The ability to adjust pressure and choose the appropriate abrasive media (such as garnet, glass beads, or aluminum oxide) provides precise control over epoxy removal, efficiently breaking down thick layers with minimal damage to the surface beneath.
One of the main benefits of Dustless Blasting is its wet, dry, and soda blasting versatility. In addition to removing epoxy, a dustless blaster can also be used for other surface preparation tasks like rust removal, paint stripping, and cleaning. This makes it a valuable, multi-use tool for industrial operations, allowing businesses to maximize the equipment's utility and reduce the need for multiple machines.
While Dustless Blasting is generally well-suited for large surfaces and intricate components, it may not be ideal for environments that want to avoid additional secondary abrasive waste. In such cases, mechanical methods like grinding or scraping could be more effective. However, for most large-scale epoxy removal and multi-purpose surface preparation tasks, Dustless Blasting is a powerful and efficient solution that combines both cleaning and coating removal in a single process.
Conclusion
Whether you're looking for how to remove epoxy from wood or how to remove epoxy from metal and other various surfaces, each application requires the right approach depending on the application, surface material, and the thickness of the coating. From dealing with a small, localized area to a large industrial floor, there are multiple effective methods at your disposal—from heat gun and scrape techniques for precision work to mechanical tools like grinders and shot blasters for large-scale removal. For even more delicate or detailed jobs, chemical solvents or paint thinners can offer a safe and efficient solution for softening and removing epoxy, though they require careful handling.
Dustless Blasting stands out for its versatility, providing both epoxy removal and additional surface prep in one process, making it an excellent choice for industrial environments without the use of chemical adhesive remover or a heat gun. By selecting the right method for your specific needs and taking the necessary safety precautions, you can effectively remove epoxy resin without compromising the integrity of the underlying surface, ensuring both efficiency and quality in your project.
Check out this resource to learn more about the power of Dustless Blasting for industrial coating removal, or download the catalog below to see our lineup of versatile machines.