How to Remove Mill Scale: Industrial Coatings
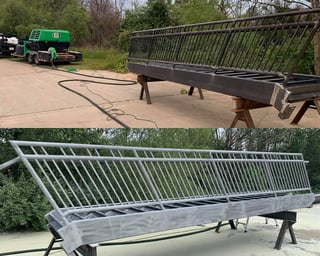
As far as heavy duty industrial coatings go, mill scale can be a stubborn one to remove. A common byproduct of metalworking, especially in industries dealing with hot rolled steel, the presence of mill scale on the underlying surface can pose problems in the finishing process. While it may seem like an insignificant aspect of metal production, understanding and managing mill scale is crucial for achieving high-quality results in manufacturing clean metal.
In this blog post, we will examine the properties of mill scale, how it is created, the negative impacts of mill scale buildup and why the removal of mill scale is crucial to guarantee the flawless surface expected in manufacturing and fabrication. We will also explore the methodology used to remove the mill scale, detailing why Dustless Blasting is widely used for this purpose throughout the manufacturing, welding and construction industries.
What is Mill Scale?
Mill scale is a flaky layer of iron oxide that forms on the outer surface of steel or iron during the hot rolling process of raw material. As the material is heated to shape it into various forms, its surface undergoes a chemical reaction with oxygen in the atmosphere due to the high temperature involved. This reaction produces a layer of iron oxides, which bonds to the steel.
Mill scale appears by way of chemical reaction as a bluish-black coating and is made up of primarily magnetite (Fe₃O₄) and hematite (Fe₂O₃). This adhering layer of iron oxides forms naturally during the manufacturing of steel and serves a protective function against further oxidation during storage. However, it also indicates the beginning of the corrosion process and the reaction continues, which can eventually have an aggressive effect on the product underneath.
Industries That Commonly Deal in Hot Rolled Steel
Hot rolled steel is a foundational material in many industries, thanks to its versatility and cost-efficiency. While its surface finish may not be as refined as cold rolled steel, its mechanical properties make it indispensable in applications where strength, durability, and large-scale production are key priorities.
Mill scale is commonly found in industries that involve steel production and fabrication, including:
-
Construction: Steel beams, girders and rebars are often coated with mill scale.
-
Manufacturing & Fabrication: The production process for metal pipes, tubes and steel billets will see mill scale as a by product.
-
Automotive & Heavy Equipment: Components for heavy machinery and automotive parts frequently develop mill scale after being hot rolled.
-
Transportation: Structural steel and other metals used in ships, car, trailer and truck chassis and railway materials often have mill scale.
-
Oil, Gas & Natural Energy: Pipework and storage tanks made from steel may see iron oxide buildup as well.
Implications of Mill Scale Buildup
While mill scale initially provides the perfect protective layer from rust, its brittle nature and tendency to crack or detach make it unsuitable for most long-term applications, especially those involving additional coatings or welding requirements. In many cases, this can end up being a major disadvantage to the finishing process as coatings applied directly might fail, so removing the mill scale becomes the only option to prevent rust.
Poor Adhesion for Coatings
Mill scale inhibits the adhesion of paints, primers, and other coatings. Its flaky texture prevents a smooth and consistent bond, leading to peeling or bubbling. This results in an uneven or failed finish as it makes way for accelerated atmospheric corrosion and reduces the aesthetic and protective quality of coated surfaces.
Welding Defects
Mill scale can interfere with welding processes as it creates a barrier between the weld material and the steel surface, leading to poor fusion. Welds may develop porosity, cracks, or weak bonds, compromising structural integrity.
Accelerated Corrosion
Mill scale can promote rust and corrosion rather than preventing it. Because of its inconsistent nature, mill scale can trap water underneath, allowing moisture to immediately start to corrode beneath the surface. Hidden corrosion can weaken steel structures over time, requiring costly repairs or replacements.
Uneven Surface and Finish
Mill scale results in an uneven texture on steel. Its rough and irregular adhesion creates inconsistencies that are especially noticeable after painting or coating. Because of this, products may not meet aesthetic or performance standards, particularly in industries like automotive or construction, and the coating applied is subject to failure.
Difficulty in Machining
Mill scale increases tool wear and machining difficulty. The hard, abrasive composition can damage cutting tools or reduce efficiency during machining operations, which can lead to higher maintenance costs for equipment and reduced productivity.
Impacts on Surface Treatments
Processes like galvanizing, anodizing, or plating are less effective on mill scale-covered surfaces. The scale prevents chemical treatments from properly bonding with the metal substrate resulting in reduced durability and lifespan on the end product.
Hindrance in Structural Applications
Mill scale can compromise structural integrity in applications requiring precise tolerances or clean bonding. Residual scale leads to inconsistent performance under stress which means increased risk of structural failure in critical applications such as bridges, buildings, or pipelines.
What is the Best Way to Remove Mill Scale?
Although mill scale is a natural byproduct of steel production and can be reused in secondary production, its presence can negatively impact metalworking processes and the durability of finished products. Removing mill scale is essential to ensure strong, corrosion-resistant, and aesthetically pleasing results.
Investing in effective removal techniques not only enhances product quality but also prevents long-term issues. The best removal method for removing mill scale depends on the size of the project, the tools available, and the surface finish desired. Not all objects will require the same removal method. In fact, effective mill scale removal often involves mechanical or chemical method—or a combination of both.
Common Methods for Removing Mill Scale
Abrasive Blasting
Using a pressure pot paired with an abrasive material like crushed glass, pyroxene, garnet or coal slag for blasting away mill scale is highly effective for surfaces involving sheets of metal or large-scale projects. This is also the preferred method to remove rust from metal, making blasting an excellent option for corrosion removal for metals that were not effectively treated after production.
Grinding
The use of power tools makes small-scale removal possible. Although time consuming and labor intensive, equipment with grinding discs, wire wheels or a rotating brush can be effective to remove the mill scale. For more info on traditional sanding and grinding methods, click here.
Pickling (Chemical Removal)
Chemical cleaning is a popular method for stripping metal of impurities. This process involves immersing steel in a chemical bath using hydrochloric acid to remove the mill scale. Acid-based solutions, such as muriatic acid or phosphoric acid, have also been used to dissolve mill scale.
Soaking mill scale in white vinegar is also a known method for scale removal, but best suited for small-scale projects. See the FAQs below for more.
Flame Cleaning
Though it is not used very frequently, applying heat via a torch to burn off mill scale has been used in the past.
Dustless Blasting for Mill Scale Removal
The Dustless Blasting technology has been proven as an effective tool for stripping almost any coating from any surface, and removing the mill scale off metal material is no different. Check out this video demonstrating the ease in which mill scale flies off using the Dustless Blasting machine.
The Dustless Blasting system can blast both wet and dry. In wet blasting applications, dust suppression by way of water helps keep the work area safe, so production in commercial and industrial settings can carry on without disruption. This is a massive advantage for metal fabrication and manufacturing plants so that production schedules can stay on track without cost prohibitive shutdowns and closures.
The capability and versatility of this blast pot technology means that any abrasive media on the market can be used for scale removal, including extremely aggressive options like pyroxene or aluminum oxide. Thanks to customizable pressure and media settings, tough coatings are no match to the great force of the Dustless Blasting machine.
To learn about the abrasive media types available on the market that can be used to remove mill scale, click here.
Recommendations for Effective Mill Scale Removal
Choose the method based on project size, budget, and finish requirements. Particularly for chemical cleaning and blasting, be sure to test on a small area to ensure desired results without over-etching the steel. Be prepared with questions for the client to understand the expectations of the final product:
- What level of surface preparation do they require? For more on NACE Surface Preparation Standards, click here.
- What coating will be applied after the scale has been removed?
- How quickly does the project need to be completed?
Abrasive blasting and chemical descaling typically require protective equipment, including gloves, goggles, and respirators; however, the Dustless Blasting system when used in a wet blasting application only requires hand, eye and ear protection.
Conclusion
It may seem like a small detail in the metalworking process, but removing the mill scale off treated metal to prep for coating is essential for creating durable, high-quality products. By understanding its formation, removal methods, and the importance of clean steel surfaces, you can ensure better results in any metal fabrication or finishing project.
For further information on how the Dustless Blasting system is specially designed to treat mill scale and other substances—particularly tough industrial coatings like epoxy, rust and more—click here. Ready to get to blasting, but unsure where to start? We've got you covered here.
FAQs About Mill Scale
Q: Can you paint over mill scale?
A: Technically you can paint over mill scale, but the paint will not adhere well and may flake off over time, especially in harsh conditions.
Q: Is mill scale hazardous?
A: Mill scale does not have a harmful effect in small quantities, but prolonged exposure to loose particles or fumes from burning or stripping mill scale can irritate skin, eyes, or lungs.
Q: Does vinegar (acetic acid) remove mill scale?
A: Yes, white vinegar works for mill scale removal by soaking for several hours, but it is more effective for small-scale applications as it is a time consuming process. If you need to remove a large amount of mill scale at a time, other methods—such as Dustless Blasting—may be more effective.
Q: Is mill scale recyclable?
A: Yes, mill scale can be collected and recycled in steel production or used in cement manufacturing as an additive.
Check out this resource to learn more about the power of Dustless Blasting for industrial coating removal, or check out our case study gallery to explore the versatility of the Dustless Blasting solution.