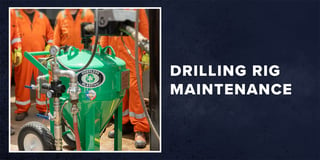
Win the Battle Against Corrosion with Dustless Blasting
Offshore rig maintenance is no small feat. Employing corrosion prevention techniques is crucial to mitigate the substantial economic impact of corrosion, which incurs $2.5 trillion in damages globally. In a world dominated by harsh environments—where saltwater, humid air, and relentless waves persistently attack steel structures—the challenge of maintaining operational safety and efficiency is unending. Corrosion remains a constant adversary, threatening to compromise the very integrity of rigs and other offshore assets. But amidst these challenges, a new wave of technology is redefining how we approach industrial coating maintenance, ensuring that these vital structures remain resilient against nature’s elements.
Understanding the High Stakes of Offshore Rig Maintenance in the Oil and Gas Industry
The offshore environment is notoriously brutal. Salt-laden air accelerates corrosion, causing extensive damage to metal structures much faster than on land. This necessitates regular maintenance to keep rigs in optimal condition, ensuring safety and operational continuity. But the traditional methods of maintenance—often labor-intensive and time-consuming—leave much to be desired. This often leads to the neglecting of asset maintenance, which can lead to costly repairs and significant impact to offshore asset integrity and personnel safety.
The Industry's Shift Towards Preventative Maintenance Tasks
In an era where minimizing costs and maximizing profits are paramount, the offshore industry has been gradually shifting towards preventive maintenance as a strategic approach. Rig managers and maintenance teams are increasingly recognizing the importance of addressing issues before they escalate into costly downtimes. Enter Dustless Blasting, a technology that’s rapidly gaining traction for its efficiency and effectiveness in preventive care.
Learn more about preventive maintenance and other maintenance strategies in our blog about plant and refinery maintenance.
Why Dustless Blasting is Revolutionizing Drilling Rig Maintenance
Dustless Blasting emerges as a game changer for fixed offshore assets, marine vessels, and other specialized equipment. Routine inspections are essential in this context to ensure operational efficiency and prevent issues. By integrating water and abrasives, this technique minimizes dust generation, making it ideal for environments where containment is crucial. Its ability to swiftly remove rust, paint, mill scale and industrial coatings ensures that maintenance schedules are met without halting operations.
See It in Action
We've put our Dustless Blasting equipment to the test on several offshore drilling rigs overdue for maintenance. Our tools have proven again and again capable of removing stubborn mill scale and thick rust layers. Eco-friendly media like crushed glass and dust suppression technology enable rig operations managers to integrate our equipment in their existing O&M strategies.
Case Study: Transforming Maintenance with the DB1500 Offshore
Our first case study showcases the effectiveness of Dustless Blasting on an offshore rig, where traditional methods proved inadequate. By using the DB1500, designed specifically for offshore environments, we achieved an SP10 near white metal finish on steel substrates. The efficient blasting process not only met industry standards but also ensured worker safety, environmental compliance, and reduced maintenance efforts through proactive measures such as regular inspections and corrosion prevention techniques.
Field Test: The New DB500 Offshore Unit
The latest iteration of our Offshore Dustless Blasting Offerings, the DB500 Offshore Unit, offers even greater advantages. Designed for safety and mobility, it features an integrated winch system, a robust cage design, and incorporates proper storage techniques to protect rig tools from damage. This unit exemplifies how innovative technology can enhance offshore maintenance by minimizing downtime and maximizing operational efficiency.
Best Practices for Integrating Dustless Blasting into Drilling Rig Maintenance Schedules
It’s clear—preventative maintenance is far more cost-effective than dealing with unexpected downtimes. Documenting maintenance activities is crucial for regulatory compliance and safety protocols. Incorporating Dustless Blasting into your maintenance program ensures ongoing asset protection and longevity. Regular use prevents severe corrosion, ultimately saving money over your offshore assets’ lifetimes.
Expert Insights on the Shift in Maintenance Practices
Renowned offshore expert sheds light on the shifting landscape of maintenance.
Traditional methods like manual grinders and scrapers are cumbersome and costly,” he notes. “Many rig managers delay maintenance until it’s urgent, leading to higher costs. Dustless Blasting offers a proactive approach, preventing problems before they escalate by incorporating essential maintenance procedures.”
Technical Insights Into Dustless Blasting
For offshore rig managers and maintenance teams, understanding the technical details of Dustless Blasting is essential. The process utilizes a water-abrasive mixture to achieve efficient material removal without generating harmful dust clouds. This not only reduces environmental impact but also enhances worker safety, making it a preferred choice for offshore applications.
Overcoming Maintenance Challenges with Innovative Solutions
In the face of challenging conditions, Dustless Blasting stands out as a reliable solution for maintaining offshore assets. Pipeline maintenance is one of the critical challenges faced, requiring continuous efforts to ensure safe and efficient operation. Its ability to swiftly remove contaminants while adhering to rigorous safety standards sets it apart from traditional methods. With this technology, offshore operators can confidently tackle maintenance tasks, ensuring the longevity and integrity of their structures.
Future-Proofing Offshore Operations with Dustless Blasting
By adopting Dustless Blasting, offshore operators can future-proof their maintenance strategies. This technology not only addresses immediate challenges but also prepares rigs for evolving industry demands. With its proven track record of reducing costs and increasing efficiency, Dustless Blasting is poised to play a pivotal role in the future of offshore maintenance.
Why Your Offshore Rig Needs Dustless Blasting Today
The benefits of Dustless Blasting are undeniable. From enhanced safety and environmental compliance to significant cost savings, this technology offers a comprehensive solution for offshore maintenance challenges. By choosing Dustless Blasting, you're not just investing in maintenance; you're investing in the future of your offshore operations.
Contact Us
Offshore rig managers and maintenance teams are invited to explore the potential of Dustless Blasting further. For more information on how to implement this cutting-edge technology into your maintenance strategy, contact Dustless Blasting today. Let's ensure your offshore assets remain resilient, efficient, and ready to face whatever challenges lie ahead.