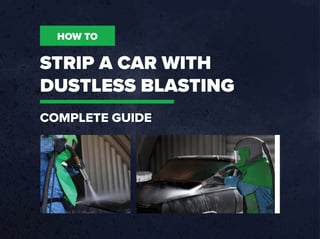
If you're looking to restore an old vehicle or just strip one down to bare metal, it's important to know how to do it the right way. One of the best ways to strip a car is with Dustless Blasting, an abrasive blasting method that's faster and safer than sanding, scraping, or using chemicals. Here, we'll provide a step-by-step guide on how to use a dustless blasting machine to strip a car including pricing, preventing rust, and cleanup.
For our complete guide on everything you need to know about automotive restoration, view this article.
Before the Job
During the quoting process it’s important to understand all of the customer’s needs. Here are a few examples:
- What finish does the customer want to achieve? Don't lose jobs because you overbid on a White Metal blast when a Commercial blast is all you need. Learn about the different surface preparation standards here.
- Will you be doing all the prep work and masking, or will the vehicle owner do it before you arrive?
- If you reveal Bondo(automotive body filler) that isn’t currently visible, are you to remove it or leave it intact?
- Will you be handling the cleanup?
- Our Dustless Blasting Rust Inhibitor will prevent flash rust after blasting for up to 72 hours. Make sure the customer has arrangements to prime the car within that time period.
When heading out to a job site, you can never be too prepared. Download our Printable Automotive Essentials Checklist.
This would also be a good time to take thorough photos of the vehicle before you start working on it, making note of any pre-existing damage.
pricing
Here are a few resources to help you develop a pricing strategy based on your projects and costs.
- How to Price Jobs [Downloadable Guide]
- How to Adjust Your Quote to Land More Jobs [VIDEO]
- Surface Area Calculators (For Pricing Jobs)
Vehicle Prep
Before blasting your car, you’ll want to mask off all rubber, chrome, plastic, glass, and electrical wires, as any form of abrasive blasting may damage them. What can’t be completely removed should be covered.
Many of our contractors like Gorilla tape for masking. However, it can leave behind a sticky adhesive mess that will be a hassle to remove. To avoid this, use masking tape or painter’s tape underneath, only overlapping by a quarter inch or so. You’ll get a strong bond that stands up to abrasive blasting, but is still easy to remove.
Note that glass can be etched just by ricochet, especially when dry blasting, so it’s important to cover all the glass, not just the edges. Cardboard is a good way to do it.
Read more containment and cleanup tips on our Academy.
Set Up Your Blast Area
Removed coatings aren’t always safe for the environment. To contain and dispose of waste properly, cover your blast area in plastic so you can roll it up and throw it away after the job.
If wind or momentum is going to carry your abrasive into sensitive areas, a simple curtain is usually enough to block it, so that it falls to the ground.
Preventing Rust
Prevent flash rust by adding the appropriate amount of rust inhibitor to your blast water before adding abrasive. It must be included in the blast water and in the final rinse water to be fully effective.
Safety
Of course while blasting you need to wear proper protective equipment, at least a face shield, gloves and hearing protection. We recommend starting with the air conditioned Nova 3 Comfort System.
General Blasting Technique
When blasting, it’s more efficient to hit the surface at an angle rather than straight on, that way you’re sort of peeling paint off, rather than just pounding it in. A 30 to 40 degree angle is good.
You also want to strike a balance between removal speed and standoff distance. When close to the surface, you’ll see faster removal, but from a smaller area.
Backing off increases the blast pattern size, and allows you to move at a more comfortable pace, while more evenly distributing the pressure and friction on your panels.
Holding the nozzle 3 inches away and moving frantically to keep up will lead to unnecessary fatigue.
Protecting Thin Panels
The water in the Dustless Blasting process reduces the temperature of the blast surface, which eliminates heat related warping. However, metal can still bend under too much pressure, or stretch when friction is applied too heavily to a small area.
If you’re blasting thin or large panels like hoods or trunk lids, you’ll want to blast from farther away than you normally would, spreading out the blast pattern more.
At a 20-30 degree angle, use a sweeping motion, being careful not to linger in any one area for too long. This technique will make the removal slower, and may require multiple sweeps, but it will distribute the pressure and friction more evenly, keeping the integrity of those panels.
If you have to blast the underside of a hood or trunk, be careful not to blast through the adhesive that anchors the frame to the skin.
Rinsing / Cleanup
The final step is to rinse the car down with Dustless Blasting Rust Inhibitor. It cleans the metal, removing chlorides and other contaminants, and once it evaporates you’ll be left with a perfect paint ready surface.
The easiest way is to add the Rust Inhibitor to your water tank and use the high volume water pump to rinse the car down. You can also use a fertilizer proportioner or a pressure washer.
After the rinse, remove any pooled liquid still on the car so it can dry quickly. A leaf blower is the best way.
The rust inhibitor should be able to prevent rust for up to 72 hours, as long as the metal is not re-contaminated. Recontamination could come from any sort of moisture, like morning dew, or even body oils from touching it, so wear gloves when moving it.
Disposal
Finally, the easiest way to collect and dispose of the spent media is to cut your plastic sheeting into sections, and roll it up into manageable bits. If you blasted wet, letting the media dry out in the sun for a while first will make this process much easier.
see it in action
For professionals and hobbyists alike, Dustless Blasting is a great option for automotive restoration. Our line of Dustless Blasting machines provides you with the flexibility to blast dry or wet depending on the project at hand, giving you the advantage to approach each job uniquely.
Want to see real world jobs completed with the Dustless Blasting machine? Check out our latest automotive restoration case studies blog.