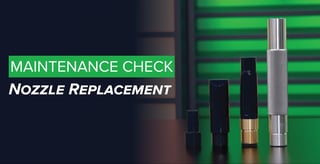
Did you know? Your sandblasting nozzle's health is a key factor in your blasting performance. In this guide, we’ll break down just how nozzle size affects efficiency and how to identify a worn nozzle. Whether you’re a seasoned professional or just starting, this knowledge will help you maximize your job speed and protect your dustless blaster from unnecessary wear.
Understanding Nozzle Size and Air Supply
Nozzles are categorized by their inner diameter, with sizes indicated by a number. This number represents the diameter in 1/16-inch increments. For example, a #5 nozzle has a 5/16" diameter, while a #6 nozzle has a 3/8" (6/16") diameter.
To determine the most efficient nozzle for your setup, consider the following factors:
- The volume of air your compressor can supply per minute (measured in CFM).
- The desired nozzle pressure (PSI) that you want to maintain for optimal blasting performance.
Refer to the nozzle chart below to select the right size for your setup.
Signs of Nozzle Wear
Nozzles naturally wear over time, and it’s important to monitor their condition to ensure optimal performance. Here are some key signs to watch for:
- You’re using more abrasive than usual.
- You notice a decrease in blasting speed or efficiency.
- Visible cracking
To further assess nozzle wear, you can perform a simple drill bit test. If a 3/8" drill bit fits through your #5 nozzle, it has worn out to a #6 size. Similarly, if a 7/16" drill bit fits, it has worn down to a #7 size, and so on. Reference the air consumption to nozzle size chart above to see if you're still in spec at a larger size. If not, it's time for a new nozzle.
Causes of Nozzle Wear
If you’re primarily using your Dustless Blasting machine for wet blasting, your nozzles will generally last longer due to reduced friction from the water mixed with the abrasive. However, no exact lifespan can be predicted, as nozzle wear is influenced by various factors, including:
- Frequency of dry blasting
- Type and size of abrasive used
- Frequency of machine use
- Nozzle lining material
It's a good rule of thumb to inspect your nozzle weekly or about every 10 work hours.
How a Worn Nozzle Affects Productivity
Using a worn nozzle can significantly impact both efficiency and cost-effectiveness. For one, it leads to increased abrasive consumption, as a worn nozzle causes excess media usage, resulting in more waste and higher costs. The blasting process also becomes less efficient, slowing progress and extending the time needed to complete a job. Additionally, higher operational costs arise, as more media and fuel are required to compensate for the reduced performance, ultimately cutting into your profit margins.
Replace your nozzle today
If you're in need of a replacement or an additional nozzle, the Dustless Blasting Online Store is your go-to source. We have a wide range of nozzles for any size DB machine to ensure you always have the right equipment for the job. Click here to replace your nozzle today. Need more information on selecting the right nozzle for the job? Check out this blog.