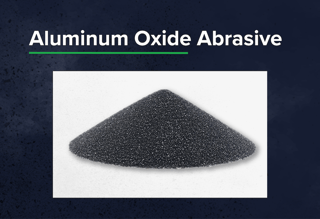
When sandblasting or abrasive blasting, there are a few key areas you can adjust to tailor your blast results to your projects: blast pressure, standoff distance, blast method (wet or dry), and abrasive type. There are many media choices on the market, so how do you know which one to choose for your project? In this post, we'll explore the pros and cons of using aluminum oxide sandblasting media (not the bonded abrasives), its applications, and key considerations for effective use.
Pros of Using Aluminum Oxide Abrasive
One of the primary advantages of aluminum oxide media is the durability. This abrasive is incredibly tough, allowing it to withstand repeated use without breaking down quickly and can be recycled multiple times depending on the type. As a result, aluminum oxide can achieve a consistent finish over time, making it a cost-effective option for projects requiring multiple rounds of blasting.
Another significant benefit is the versatility of aluminium oxide. It can be used on a wide range of materials, including metal, concrete, iron, and glass, making it ideal for various applications. Its sharp edges enable efficient material removal and surface anchor patterns, allowing for quicker project completion and longer-lasting surface coating.
Additionally, aluminum oxide is non-toxic and environmentally friendly compared to other abrasive materials, such as silica sand. This characteristic makes it a safer choice for both operators and the environment, contributing to safer workplace conditions.
Cons of Using Aluminum Oxide Blasting Media
Even with its many benefits, aluminum oxide abrasives do have a few downsides. One key drawback is the cost; while it’s tough and durable, you’ll usually pay more upfront compared to other abrasives.
Another thing to keep in mind is the potential for dust. When you’re blasting with aluminum oxide, it can kick up a fair amount of fine dust, which means you might need extra ventilation or dust collection systems to keep things safe. You can also switch to a wet blasting method to further suppress the dust plume and facilitate a low dusting work environment.
Plus, because aluminum oxide is quite abrasive, it can damage softer materials if you’re not careful. That means you need to choose the right abrasive and handle it with precision to avoid accidentally harming your workpiece.
Applications of Aluminum Oxide Blasting Abrasive
The intense hardness and angle of the abrasive makes this media the perfect solution for tough materials like concrete, iron, and more. Aluminum oxide is widely utilized across various industries, making it a go-to choice for many professionals. For automotive parts, industrial steel, iron, and other metal fabrication items, aluminum oxide's hardness and low friability allow it to withstand heat buildup during dry blasting while retaining its angular shape for an efficient and consistent blast pattern for removing rust or mill scale.
When blasting solid wood, plywood, or other wood-based materials, the sharp edges and toughness of aluminium oxide are ideal for creating a raised-grain finish on the material or etching the wood. If you're looking for light stain or paint removal on your wood surface, you might want to opt for a less-harsh abrasive such as corn cob.
Operators can also utilize aluminium oxide to etch plastics like acrylic, polycarbonate, and PVC with a frosted finish. Be sure to conduct a test blast to dial in your abrasive grit, color, blast standoff distance, and blast pressure before beginning a project to ensure you're achieving your desired finish.
Another popular substrate for this abrasive is ceramic or glass. With the tough, angular shape of this abrasive, blasters can create decorative finishes or designs in glass with precise detail.
Key Considerations When Using Aluminum Oxide
There are a few points to consider when choosing to blast with aluminum oxide blasting media. For best results, consider the following:
- Grit Size Selection: Choosing the appropriate grit size is crucial. Coarser grits are best for heavy material removal, while finer grits are suited for achieving smooth finishes. Understanding project requirements will guide you in selecting the right grit.
- Types of Aluminum Oxide: There are three primary types of aluminum oxide sandblasting abrasives:
- White Aluminum Oxide: The purest form, known for high friability and sharp cutting edges, ideal for precision applications like polishing and etching.
- Pink Aluminum Oxide: Slightly less pure, this type is known for its durability and consistent performance, often used for general-purpose blasting and surface preparation.
- Brown Aluminum Oxide: The most economical option, featuring a rougher texture and greater toughness, making it suitable for heavy-duty tasks like coating removal and metal finishing.
- Equipment Settings: Proper equipment settings are essential. Adjusting pressure and nozzle size based on the material being worked on is critical to avoid damage and ensure efficiency. Operators should also be trained in best practices for sandblasting to maximize safety and effectiveness.
- Blasted Substrate: Because of the hardness and angular shape of aluminum oxide, use caution when blasting to prevent unwatched damage to the substrate. For softer materials, you might want to choose a softer and more round media.
Conclusion
Aluminum oxide sandblasting media offers a powerful combination of hardness, durability, versatility, and recycled ability, making it a popular choice across various industries. Its ability to provide consistent finishes makes it ideal for working with and etching metals, concrete, plastics, ceramics, and glass. While the upfront cost may be higher, the long-term benefits, including durability and recyclability, often justify the investment. To maximize effectiveness, it’s crucial to select the right grit size, understand the different types of aluminum oxide, and adjust equipment settings accordingly. By keeping these factors in mind, aluminum oxide can enhance your surface preparation and finishing results significantly.
For more information on selecting the best abrasive for media blasting, check out this blog.