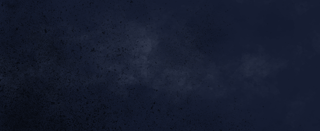
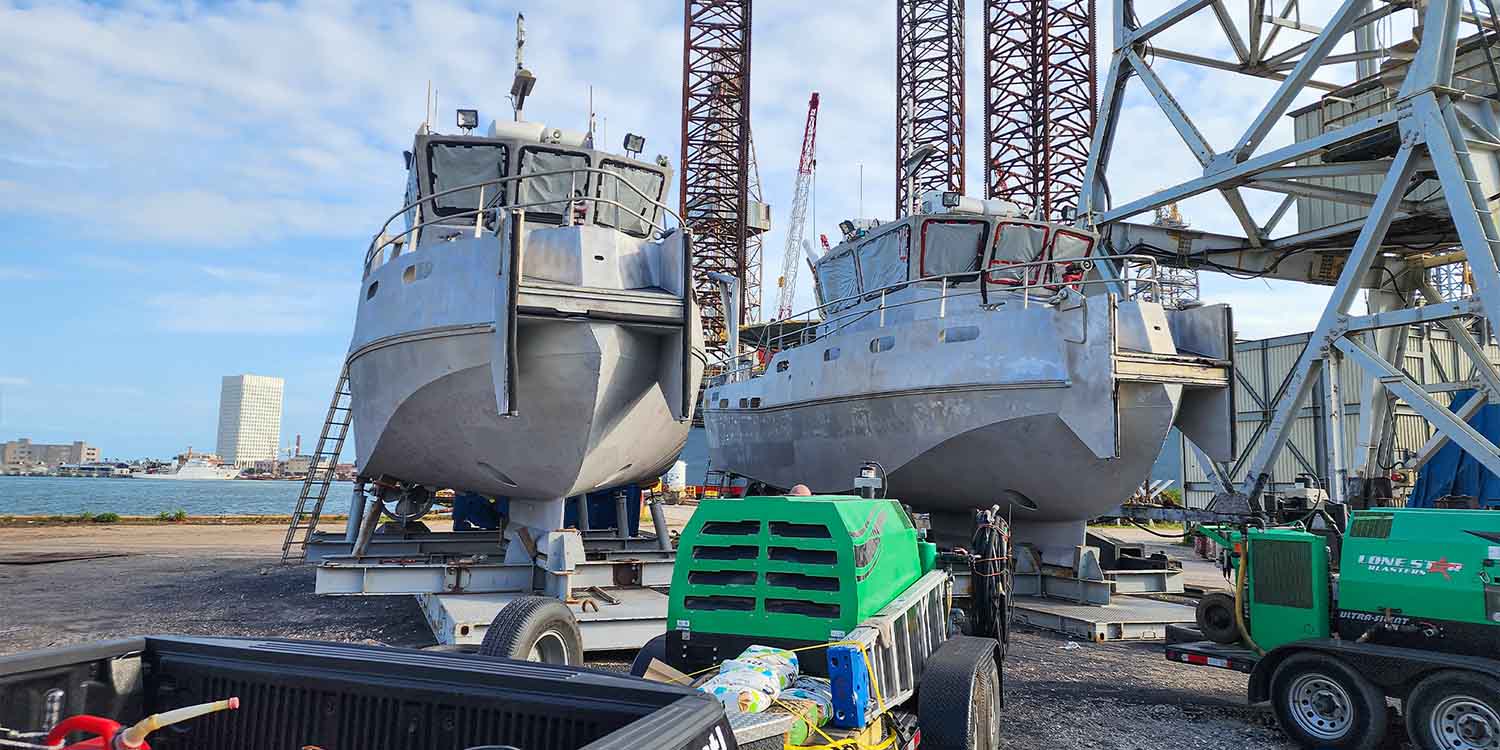
In an impressive feat of teamwork, two Texas-based blasting companies joined forces to rid two 40-foot metal boats of marine paint, anti-fouling, and bondo in less than a day.
We improved a major shipyard's blasting productivity by over 30% by implementing our unique DUSTLESS BLASTING® technology.
Dive into the details of our field test below.
The owner of a prominent marine repair shipyard on the Mexican Pacific coast had significant productivity concerns due to the dust production from their dry blasting processes.
At their request, we embarked on a series of experiments in order to quantify exactly the benefits of upgrading their shipyard's dry sandblasting equipment to DUSTLESS BLASTING® equipment.
We began by recreating the exact conditions of the marine coatings they employ at our facility in Houston.
We spoke with the shipyard's parent company, who mainly operates in the Tuna fishing and processing industry. We learned that their critical vessel maintenance operations are performed between October and February (4 months).
DUSTY WORK ENVIRONMENT
We visited the shipyard and learned about their problems with dust containment during their dry blasting operations, which often force nearby workers to leave the area and only resume their work once blasting is complete. They expressed their interest in a wet blasting system like ours, which could greatly improve their productivity (and reduce overall cost) by eliminating the dust problem altogether.
A total of 3 coats of Hempel epoxy paint were applied to reach an average coating thickness of 18 mils.
Using different combinations of abrasives, nozzles, blast pressures, and abrasive flow configurations, the times required to remove 1 sqft. of coating were measured.
The total area was prepped, treated with marine epoxy paint, and then divided into three segments of 9m2 (96.9ft2) each for the following tests:
The experiments were carried out dry and wet with:
Our main takeaway is that wet blasting with copper slag (their abrasive of choice) is significantly speedier than dry blasting. The tremendous advantage of transitioning their equipment line to dustless blasting cannot be emphasized enough, as it is not only faster, but also suppresses dust, enabling nearby workers to carry on with their tasks uninterrupted.
In this field test, Dustless Blasting provided a 31.82% increase in coating removal speed compared to dry blasting.
Fill out the form below and get a printable document of our findings with even more insights.
Investing in this versatile machinery will streamline operations and boost profitablility. No longer are you having to waste time and money on outdated methods or outsourcing.
Whether it's used to restore classic cars, boats, or antiques - the applications for dustless blasting are seemingly endless and can help existing businesses expand their offerings and generate increased income.
Dustless Blasting can strip away unwanted, tough coatings from surfaces. Our machines offer an advantage over traditional sandblasting – significantly less dust and more productivity per pound of abrasive.
In an impressive feat of teamwork, two Texas-based blasting companies joined forces to rid two 40-foot metal boats of marine paint, anti-fouling, and bondo in less than a day.
A swift solution was needed when blisters were discovered on the fiberglass gelcoat of this 54-foot vessel. And that's where Dustless Blasting stepped in as the clear choice.
Two blasting companies collaborated and leveraged DUSTLESS BLASTING® equipment for an industrial-scale water treatment plant project.