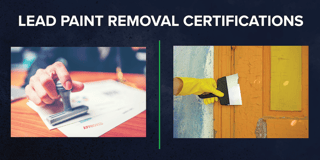
Lead Paint Paint Removal Certification: What You Need to Know
The presence of lead-based paint on painted surfaces brings with it a host of regulations that professionals must follow to avoid exposure to this health hazard. Because of the seriousness of this substance, the removal of any lead-based paint in structures built prior to 1978 requires certified renovators with a lead paint removal certification, such as the EPA Lead Paint Certification.
This blog covers why lead paint removal and disposal certifications matter, and what agencies like the EPA and OSHA require for those looking to become certified abatement supervisors.
Why Are Lead Based Paint Certifications So Important?
Although banned for residential use in 1978, lead-based paint is still found in older buildings. As it deteriorates, it can release hazardous dust and chips—posing serious health risks, especially to children and workers. Professionals working on pre-1978 structures must have a lead certificate to ensure safe, compliant practices in abatement projects.
Proper certification ensures that those who handle or remove it are trained to conduct abatement activities that minimize lead exposure. Failing to comply with federal, state, or local laws can result in steep fines and even legal action. For more on how to identify and remove lead paint, click here.
Who Oversees Lead Paint Removal & Disposal Regulations?
Lead paint removal and disposal are regulated by several government agencies, each with a different focus and process to become lead paint certified:
EPA (Environmental Protection Agency)
The EPA enforces the Renovation, Repair and Painting (RRP) Rule, which requires training and certification for anyone who disturbs paint in pre-1978 homes or child-occupied facilities. According to the EPA, firms must be Lead-Safe Certified and individuals must complete an 8-hour Lead Renovator Certification course. Becoming EPA lead certified helps protect the public from exposure risk.
OSHA (Occupational Safety and Health Administration)
While the EPA protects the public, the Occupational Safety and Health Administration (OSHA) focuses on worker safety as it pertains to lead abatement activities under the Lead in Construction Standard (29 CFR 1926.62). Under OSHA, employers must assess lead exposure risks on job sites. Required measures include personal protective equipment, training, and blood lead level testing for employees. The implementation of risk assessment activities and hazard screenings help determine if you need to perform inspection or if post-abatement clearance activities are needed.
Beyond Federal Regulations
In addition to EPA and OSHA rules, state or local governments may have stricter training requirements to perform work in this space—especially around disposal. State and local regulations can include specific abatement methods, waste handling protocols, and licensing for abatement workers. Understanding these rules is crucial for staying compliant and protecting your team and clients.
Seek council from EPA authorized state environmental or health department for guidance on following requirements.
Understanding Lead Based Paint Abatement and Disposal Certifications
Lead abatement certification ensures that contractors know how to handle, dispose, and compile abatement reports of lead-containing materials. Post-lead based paint abatement clearance activities are essential for individuals who wish to carry out inspections and file abatement reports. Proper disposal typically involves:
-
Collecting and Bagging Waste: Placing paint chips, dust, and other debris in heavy-duty bags or containers, labeled to indicate lead content.
-
Transporting Waste Safely: Depending on your state, you may need special permits or to use certified haulers for transportation.
-
Using an Approved Facility: Disposal usually requires a landfill or facility authorized or certified to handle hazardous or special wastes.
Although federal guidelines via the EPA and OSHA are your primary references, be aware that your specific state might have different thresholds for hazardous waste classification. When in doubt, consult state environmental agencies and/or local municipalities.
Steps to Getting Certified
-
Choose an Accredited Training Provider: Look for EPA lead paint certification courses in your region. Local or state environmental agency websites often have lists of accredited programs.
-
Complete the Required Training: Expect hands-on instruction about safe work practices, PPE usage, dust containment, cleanup, and disposal in order to receive a course completion certificate.
-
Apply for Your Firm Certification: After receiving your completion certificate for individual training, the business must also become an EPA Lead-Safe Certified Firm.
-
Renew Certifications & Pay Applicable Fee: These certifications typically aren’t lifelong. Check expiration dates and plan to re-certify and pay the applicable fee before they lapse.
The core requirement for individual certification is a Renovation, Repair and Painting (RRP) course from an EPA-accredited provider. For related professions like general contracting or building construction, lead based paint activities training is essential.
Maintaining Lead Certification
Lead certification requires ongoing commitment to stay compliant. Certification is valid for five years, after which a refresher course must be taken to renew the completion certificate. The refresher course, typically a half-day session, covers the latest regulations and best practices for lead-safe work. To maintain lead certification, individuals and firms must:
-
Complete a Refresher Course Every Five Years: This ensures that you stay updated with the latest safety protocols and regulatory changes. Ongoing training in lead hazard management is essential for maintaining certification and ensuring safety.
-
Stay Up-to-Date with Regulations: Regularly review and understand any new guidelines or changes in safe work practices.
-
Follow Lead-Safe Work Practices: Continuously implement the practices learned during training to minimize lead exposure risks.
-
Maintain Accurate Records: Keep detailed records of all training and certification activities to demonstrate compliance during inspections.
By maintaining lead certification, professionals can ensure they are equipped to handle lead-based paint safely, protecting themselves, their clients, and the environment from the dangers of lead exposure.
Penalties for Non-Compliance
Failing to comply with lead-based paint regulations can result in severe penalties. The EPA has the authority to impose fines exceeding $37,500 per violation per day. In recent years, numerous companies and individuals have faced fines ranging from $1,000 to $500,000 for non-compliance. The consequences of non-compliance include:
-
Fines and Penalties: Significant financial penalties can be imposed for each day of violation.
-
Loss of Business Licenses: Repeated violations can lead to the revocation of business licenses, halting operations.
-
Damage to Reputation: Non-compliance can tarnish a company’s reputation, leading to a loss of trust and business.
-
Health Risks: Failing to follow safe work practices and lead exposure can result in serious health risks for workers and occupants, including neurological and developmental issues.
To avoid these penalties, it is essential for individuals and firms to obtain lead certification and adhere to lead-safe work practices, ensuring a safe and compliant working environment.
How Dustless Blasting Makes Lead Paint Removal Safer
While certifications and regulations set the groundwork for a safe job site, the tools you use can make all the difference. Traditional removal methods like sanding or dry blasting often release hazardous lead dust into the air, while Dustless Blasting uses water to suppress dust at the source, making lead paint removal both safer and more efficient.
Before any abatement project begins, a lead hazard screen is essential. This identifies potential exposure risks, informs your containment plan, and ensures proper post-abatement clearance procedures.
Why Dustless Blasting Is a Smart Choice for Lead Abatement
Lead paint removal is a serious responsibility—and one that demands both proper certification and smart job site practices. Understanding and complying with EPA, OSHA, and local regulations is only the beginning. Choosing a method like Dustless Blasting that aligns with those safety standards helps you work more efficiently, reduce risk, and protect both your team and your clients.
Dust Suppression: The water and abrasive mix captures particles before they become airborne, dramatically reducing lead dust.
Efficient Coating Removal: Removes paint, rust, and other coatings quickly—without the intense manual labor of sanding or scraping.
Reduced Containment Requirements: Less dust means simpler, more cost-effective containment strategies.
Surface Versatility: Dustless Blasting is effective across a wide range of surfaces including concrete, brick, metal and wood.
Dustless Blasting is committed to helping you maintain a safe, efficient job site. Our equipment reduces airborne dust and meets the demands of lead abatement projects—all while saving you time and money on labor. If you have questions about how Dustless Blasting can support your certified lead removal and disposal efforts, reach out to us anytime. We’re here to help guide you to the best solutions for your business.
Resources and Support
United States Environmental Protection Agency (EPA): Comprehensive guidance, training, and certification programs for lead safety practices.
National Lead Information Center (NLIC): Information on safe work practices and local abatement programs.
Occupational Safety and Health Administration (OSHA): Requirements and regulations for worker safety.
Disclaimer: This post is for informational purposes only and does not constitute legal advice.