Comparing Dustless Blasting to Laser Cleaning
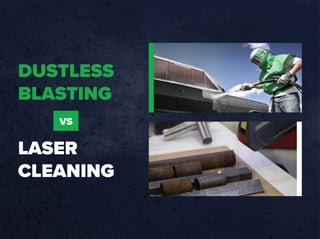
Laser cleaning has grabbed the internet by storm recently, and for good reason! It's incredibly satisfying to watch rust, paint, or other contaminants virtually disappear from a surface like magic. But how does it work? And why isn't everyone using them?
The laser cleaning process is cutting-edge and fascinating, but like any surface preparation method, has it's limitations. Let's take a look at laser cleaning, how it works, its advantages and disadvantages, as well as what you should consider when choosing your surface preparation method.
How does laser cleaning technology work?
Laser cleaning - more commonly referred to as laser ablation - is the non-contact process of removing material from a surface by irradiating it with a high-powered laser beam, creating shockwaves that eject contaminants or turn them into gas. After being removed from the surface, the debris is then evacuated through a fume extraction system.
The benefits of laser cleaning
When used correctly, a high-power cleaning laser will remove rust, oil, and other coatings without damaging the substrate. This is especially valuable for applications where the surface needing treatment has historical value. Additionally, there is no use of water or solvent and overall is an environmentally friendly process.
When combined with robotics, laser ablation becomes a highly controllable and flexible process, which can be extremely valuable as part of a production line. Automotive, aerospace, and defense manufacturers are benefitting from the cost-saving advantages that come with incorporating automated laser systems for rust removal, paint removal, substrate texturing, laser annealing, and more.
The drawbacks of laser cleaning
Everything comes at a cost. And while there are large manufacturing operations that can accept the high initial expense of laser technology, it just isn't a cost-effective solution for the everyday small business owner providing surface cleaning and surface preparation services.
Read more about laser cleaning equipment costs.
While there's a place for laser cleaning in many industrial applications, it isn't a one-size-fits-all solution. To operate at the level of efficiency needed to be competitive and profitable, laser systems are often custom-built specifically for the system they're being incorporated into. While this application-specific model works at scale, it isn't very flexible. And while laser ablation can be achieved manually with a custom-handheld device, giving it more flexibility to tackle a variety of applications, you can expect other traditional cleaning methods to achieve similar results faster or at a cheaper cost to customers.
The limitations of lasers also begin to show with tougher jobs, like removal of thick materials over a large area. Laser cleaning simply isn't as efficient at cleaning heavily-corroded surfaces. And for thicker layers of coatings, heat buildup can be a problem. Burning through layers of dried paint with a high power laser beam can cause that paint to ignite.
For example, if you need to remove rust, our laser units will do so at a much faster rate than if you had to remove very thick coatings over a large area. By the same token, flat surfaces will experience better results than if you have to clean surfaces with limited line of sight. This doesn’t mean that laser technology only works on simple tasks. We do provide techniques for complex, 3D surfaces, but removing layers with a thickness of more than 0.5mm tends to not be cost effective.
-AdaptLaser, How Laser Cleaning Works
Without a fume extraction system in place, operator safety is also a significant concern. When cleaned with a laser, toxic contaminants and chemicals can result in toxic fumes which must be extracted and disposed of properly.
Is laser cleaning the right surface preparation method for you?
It's clear that while this technology isn't the appropriate method for every job or business, it can really excel in some circumstances. If you're considering adding laser ablation to your arsenal of surface preparation methods, ask yourself these questions:
What are you trying to achieve?
If you're looking to remove surface rust, paint, or other coatings without damaging the substrate, laser cleaning is a great option. If you need to remove tough, thick coatings over a large area, traditional removal methods like abrasive blasting may be a better choice.
How much money are you willing to spend?
Laser cleaning equipment is expensive. If you're not prepared to make a significant initial investment, it may not be the right choice for your business. Consider whether the advantages listed above outweigh the disadvantages for your specific application.
How much time do you have to complete the job?
Laser blasting machines may take longer than other methods to complete a task due to their precision.
How much flexibility do you need?
Tough jobs often pay the most. Laser cleaning machines are only at their best in a controlled environment, cleaning flat or close-to-flat surfaces. Consider the additional flexibility and performance that other methods afford you in your day-to-day operation.
The parts’ geometry should also be contemplated. Because the ablation process works by targeting a beam of light on the surface, that surface needs to be accessible to the scanner, which is difficult when it is necessary to reach inside small crevices.
-Production Machining, Is Laser Cleaning Beneficial for Your Application?
Does the substrate need an anchor profile?
The anchor profile or anchor pattern refers to a series of “peaks and valleys” that exist on a substrate. This surface roughness, often microscopic in scale, is extremely important to ensuring that new coatings adhere properly. Some laser cleaning machines are now able to create an anchor profile, but this is often seen as a secondary function called laser pretreatment. If you're in the business of preparing surfaces for recoating, you'll want to consider other methods that may do a better or faster job.
With an abrasive blasting machine, for example, you can clean a surface and create an anchor profile all in one step. This makes it a much more efficient and effective preparation solution for many businesses.
Whether you're looking to provide rust removal, paint removal, or other surface cleaning services without damaging the substrate, laser cleaning is a potentially great option - but it isn't right for every business. Consider the details above when deciding whether a laser cleaning machine is right for you.
How Does Dustless Blasting compare to laser technology?
Versatility and Flexibility
Dustless Blasting machines are capable of using all types of abrasive material. Wet or dry, sand or soda, garnet or recycled glass, even biodegradable media such as corn cob or walnut shells. All of these abrasives can run through the same machine and by merely adjusting the machines pressure, you can handle various industry applications. There is no other machine in the world with such a wide range of capabilities and it's easy to use.
Abrasive blasting can handle tough jobs with ease. Blast through layers of tough coating and profile a surface all in one step, with no heat-related warping or flash rust. The bottom line is - you can say yes to far more jobs using a Dustless Blaster than with a laser cleaning machine.
Affordability
Laser cleaning machines are infamous for their extreme prices and that isn't expected to change anytime soon.
We do not expect the price of Laser systems to fall over the next 5 years from this current new generation and technology. The knowledge needed to manufacture components and systems is highly specialized and there is no room for any significant price drops. Even since COVID started our materials cost has risen, once our manufacturers stocks have depleted, increases may even rise.
-LaserIndustries, FAQ's
With Dustless Blasting, own an entire mobile business for as little as $50,000. Since Dustless Blasting allows you to make more in an hour than many people make in a day, it truly pays for itself in no time. Plus, financing is available so you can started right away.
Reliability
When you need machines that just won't quit, no matter what you throw at them, you need Dustless Blasting.
-
Blast pots are backed by a lifetime warranty.
-
Equipment is made in the USA, to the highest industry standards, and is rigorously tested.
-
A simple system with few wear parts, and no proprietary valves.
-
Get full factory support on all equipment: online training, support, and parts store.
Equipment downtime is expensive. And calling a technician out to your jobsite to repair specialized equipment every time something goes wrong is a major expense people often forget about. At Dustless Blasting, we give you the knowledge to maintain and repair your blasting equipment. Our machines are designed to be easy to repair and contain no proprietary valves.
The Mobile Advantage
Go where the business is. With a Dustless Blasting mobile trailer, you have the ability to bring your blasting services to any job site. With mobility comes additional opportunity to meet the needs of your customers, resulting in more revenue potential for your business.
-
Self-contained equipment is made to move.
-
Everything you need to blast on-site is mounted on a purpose-built trailer.
-
Includes a powerful compressor, large water tank, spacious toolboxes, auxiliary air ports and more.
Support
Benefit from a community of business owners, marketing support, and a trusted brand to help you along the way.
In Conclusion
Laser cleaning is an exciting newer technology that excels at certain tasks like surface rust removal, but due to a variety of factors, simply isn't the right tool for most applications. If you're considering a new surface preparation method for your business, a Dustless Blasting machine is likely the better choice for you.