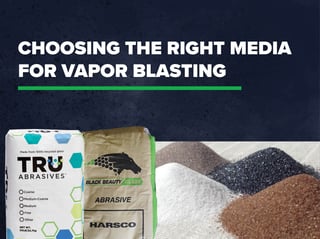
Vapor blasting, also known as wet blasting or vapor honing, is a surface preparation process that involves the use of an abrasive media combined with water to remove coatings from a variety of surfaces quickly and safely with pressurized air. Choosing the right abrasive media is crucial to the success of the vapor blasting process. In this blog post, we will explore the best abrasive media to use for vapor blasting.
How is Vapor Blasting Used?
Vapor blasting can be used for a variety of applications, including surface preparation, cleaning, and restoration. It is commonly used in the automotive industry for cleaning engine parts, carburetors, and other components. It is also effective in removing coatings and cleaning delicate components that traditional abrasive blasting methods might further damage.
What is the Best Media to Use for Vapor Blasting?
When selecting a media for vapor blasting, it's essential to ensure that the abrasive is clean, uniform, and capable of sinking in water. The best media to use for vapor blasting depends on the application and the desired finish. Crushed glass abrasive is our number one choice for removing coatings as it is clean, chemically inert and can be used for a wide variety of applications. If you're needing a round abrasive for cleaning purposes, we recommend going with glass beads.
Media Type
The type of abrasive media used in wet blasting can also impact the process. Different media types have varying levels of hardness, density, and shape, which can affect their cutting ability and impact on the surface. Some common media types used in wet blasting include glass beads, garnet, crushed glass and aluminum oxide.
Types of media you can use for vapor blasting
Crushed Glass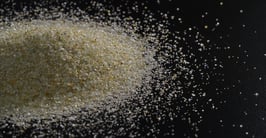
Crushed glass blast media is free from crystalline silica and made from 100% recycled glass. This is an efficient abrasive that has an angular profile which is great for removing a wide variety of coatings on many different surfaces. It produces a cleaner finish than most slags and is very cost conscious.
Aluminum oxide
Aluminum oxide is one of the most commonly used abrasive media for vapor blasting. It is a versatile abrasive that is suitable for use on a wide range of materials, including aluminum, steel, and other metals. It is also very durable and can be reused multiple times before needing to be replaced. Aluminum oxide is available in a range of grit sizes, from fine to coarse, making it suitable for use on a variety of surfaces.
Garnet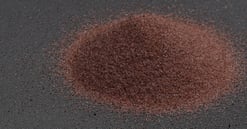
Garnet is another popular choice of blast media for vapor blasting. It is a hard, dense material that is well-suited for removing heavier deposits of rust and corrosion. Garnet can also be used to create an attractive satin finish on metal surfaces.
Glass beads
Glass beads are another popular choice for vapor blasting. They are made from soda-lime glass and are very uniform in shape and size, which makes them ideal for use on delicate surfaces such as aircraft components and medical equipment. Glass beads are also very environmentally friendly and can be reused many times before needing to be replaced.
Plastic media
Plastic media is a non-abrasive media that is ideal for use on soft metals such as brass and aluminum. It is also suitable for use on plastics and composites. Plastic media is very gentle and does not damage the surface being cleaned or prepared. It is also very environmentally friendly and can be reused many times before needing to be replaced.
Choosing the right abrasive media is crucial to the success of the vapor blasting process. Aluminum oxide, glass beads, silicon carbide, plastic media, and crushed glass are all excellent choices, depending on the material being prepared or cleaned. Each of these abrasive media has its unique advantages and disadvantages, and the choice of media will depend on the specific requirements of the project. By choosing the right abrasive media, you can ensure a smooth and even finish that will meet your expectations.
Creating the right anchor profile
The characteristics of the wet blasting process, particularly the nozzle size, angle, flow rate, and media type, can be adjusted to achieve the desired results for a particular surface preparation application. Careful consideration of these factors can help to optimize the efficiency and effectiveness of the wet blasting process.
Nozzle Size
The size of the wet blasting nozzle is a crucial factor that determines the flow rate and velocity of the mixture. A smaller nozzle size will increase the pressure of the mixture, resulting in higher velocity and more aggressive blasting. Conversely, a larger nozzle size will lower the pressure, resulting in lower velocity and gentler blasting action.
Nozzle Angle
The angle at which the nozzle is held can also affect the wet blasting process. A nozzle held perpendicular to the surface will result in a more even distribution of the abrasive media and water mixture. Tilting the nozzle can direct the flow of the mixture in a specific direction, allowing for more precise blasting in certain areas.
Flow Rate
The flow rate of the water and abrasive media mixture is another crucial factor in wet blasting. A higher flow rate will result in more material being removed from the surface but may also cause excessive erosion of the substrate. Lower flow rates will be less aggressive but can be more precise and cause less damage to the substrate.
What is the safest media for Vapor Blasting?
When it comes to safety, certain abrasive media are safer to use than others. For example, plastic media and crushed glass are non-toxic and do not produce harmful dust particles when used for vapor blasting.
It is important to consider the environmental impact of the abrasive media used for vapor blasting. Some abrasive media, such as glass beads and plastic media, are environmentally friendly and can be reused many times before needing to be replaced. Others, such as silicon carbide, can be harmful to the environment and should be disposed of properly.
What Applications Is Vapor Blasting Best Suited for?
Vapor blasting is best suited for applications where a surface needs to be simultaneously cleaned and prepped as this process can remove coatings while cleaning the surface. It is also the only method that reduces dust. If you need to blast in an area with others nearby, vapor blasting is the process to go with as it reduces dust plumes up to 95% – resulting in a safer environment for workers and bystanders. Vapor blasting is also preferred when removing heat-reactive coatings that would melt with traditional dry blasting. The cooling effect by adding water helps prevent thin metals from warping, weak substrates from cracking, and heat-reactive coatings from melting. It is commonly used for aerospace, automotive, concrete, and marine restoration.
Ultimately, the choice of abrasive media for wet blasting will depend on the specific application and the characteristics of the surface being prepared. Careful consideration should be given to factors such as the level of surface finish desired, the potential for water damage, and any health and safety risks associated with the abrasive media. For a complete guide on choosing the right abrasive, whether vapor blasting or dry blasting, view this blog.